10 claves para obtener un buen teñido con colorantes reactivos
- Ing. Arnaldo Peña C.
- 20 oct 2017
- 11 Min. de lectura

La tintura de fibras celulósicas (algodón, lino, yute, ramio y otras fibras regeneradas como viscosa, modal, lyocell, tencel) en la actualidad se realiza tiñendo con colorantes reactivos, principalmente cuando se trata de telas para la fabricación de prendas de vestir; esto debido a la alta solidez al lavado que presentan estos colorantes (solidez = permanencia del color en el material textil). En base a mi experiencia, he sintetizado 10 pautas que te servirán como herramientas para obtener un teñido de alta calidad.
Es importante entender que el teñido reactivo se constituye de 4 etapas muy diferenciadas que son:
a) Pretratamiento
b) Absorción
c) Reacción
d) Enjabonado o eliminación del hidrolizado
1. CALIDAD DEL PRETRATAMIENTO
Debemos asegurarnos de que el pretratamiento sea realizado de manera óptima y garantice un buen teñido posterior (teñido bien igualado, libre de manchas, evitando precipitados). Para ello se debe controlar los siguientes parámetros al final del proceso de pretratamiento y antes de iniciar el teñido.
pH de la tela: Debe estar en un rango de 6.5 – 7.0, esto se realiza de forma más exacta haciendo un pH de extracción a la tela y de forma práctica o simplificada midiendo el pH del baño residual, sea con potenciómetro o papel indicador. De estar en el rango alcalino podría generarse una reacción anticipada del colorante, lo cual no es deseado en esta etapa y de estar en el rango ácido impide la deseada reproducibilidad del color.
Grado de blanco del sustrato: Deberá ser igual al grado de blanco obtenido en laboratorio con el cual se ha formulado la receta, esto permitirá la reproducibilidad del color de laboratorio-planta.

Residual de peróxido: cuando se ha realizado un pretratamiento oxidativo con peróxido de hidrógeno es imprescindible realizar su eliminación con un agente reductor como el bisulfito de sodio o la catalasa para obtener un residual de peróxido = 0; este es el valor que debe tener el baño antes de la tintura, en caso contrario el peróxido residual va a reaccionar con el colorante, destruyendo al cromóforo y haciéndole perder sus propiedades (esta medición se hace con un papel indicador).
Hidrofilidad del sustrato (tela, hilo, prenda): Deberá ser buena, esto nos garantiza que la eliminación de las grasas y ceras naturales contenidas en el algodón u otras fibras naturales hayan sido removidas apropiadamente, caso contrario cabe el riesgo de una tintura defectuosa; para su comprobación basta dosificar una gota de agua sobre el material pretratado seco, la gota debe ser absorbida en un tiempo no mayor a dos segundos y debe formar una circunferencia; caso contrario el pretratamiento deberá ser reforzado antes de iniciar el teñido. Otra forma adicional y más convincente de evaluar la calidad del pretratamiento es por la medición de la capilaridad: esto se realiza sumergiendo en posición vertical un extremo del material pretratado en una solución de colorante (material de 15 cm x 2 cm). Un sustrato bien tratado permite que el colorante suba por lo menos 2 cm en un minuto, de preferencia realizarlo en una solución de 2 g/l de colorante turqueza, este colorante por ser una ftalocianina de molécula grande es el más dificultuoso de lograr una rápida difusión.
2. TIEMPO DE ROTACIÓN DE CUERDA O TIEMPO DE VUELTA (en caso de teñido a nivel laboratorio o teñido en prendas de vestir su equivalencia vendría a ser: LA AGITACION).
a) El tiempo de rotación (tiempo de vuelta) está referido al teñido de telas en género de punto; el cual se realiza en máquinas de teñido Overflow, Jet o Multiflow, las cuales están dispuestas de torres / toberas y canastillas donde se arman cuerdas; estas cuerdas son la unión de punta-cola de varios rollos (rollo = unidad de producción de tejeduría, equivale a 20 kg - 25 kg de material). Una cuerda puede estar formada desde 1 a 10 rollos, dependiendo de la capacidad y diseño de la máquina.

Es importante para un teñido reactivo que la cuerda complete su tiempo de vuelta en un periodo no mayor a 2 minutos (t=2min). Hemos determinado experimentalmente que un tiempo de rotación mayor a 2 minutos, puede generar problemas de desigualación, degradé, manchas, color disparejo; si bien es cierto que no es una regla absoluta ya que depende de las características del colorante, del tipo de tejido y otras variables; lo importante es trabajar en el rango más confiable posible.
También es importante que los tiempos de vuelta sean similares entre todas las cuerdas, cuando éstas son muy diferenciadas entre sí, se obtienen tonos diferentes entre cuerdas.
b) La agitación, conceptualmente podemos considerarla el equivalente al tiempo de rotación de cuerda, su importancia radica en que un buen teñido uniforme, requiere de una agitación constante en máquinas frontales, sean estas máquinas de laboratorio (se tiñe muestras de tela) o en Lavandería Industrial (se tiñen prendas de vestir) y se controla mediante las revoluciones por minuto (rpm) de las máquinas.
Con carga baja = 30 rpm
Con carga alta = 45 rpm
Estas máquinas deben tener un doble sentido de giro (Ejemplo: de 2 min en sentido horario y 2 min en sentido antihorario), a esto se le llama ciclo.
Tampoco es una regla general, pero es un buen punto de partida, dependiendo del tipo de material, pueden experimentar variación de las rpm así como el tiempo del ciclo.
3. CONTROL DE LA RELACIÓN DE BAÑO (R:B)
Es el volumen de agua a utilizar por kg de tela teñido (l/kg), aunque pareciera fácil su control es muy importante realizarlo, validarlo y verificarlo, respecto a lo formulado en laboratorio, sobre todo en máquinas automatizadas donde es necesario calibrar los instrumentos de medición como flujómetros, caudalímetros, cuentalitros y sobretodo, tener presente los descuentos de volumen, por el factor de absorción del material (cuando se inicia el teñido con una base húmeda).
El control de la R:B incide principalmente en la reproducibilidad del color de laboratorio a Planta y la repetibilidad del color de lote a lote (batch a batch). Esto es muy importante cuando se quiere una alta productividad y confiabilidad en los procesos de tintura.
Las relaciones de baño, varían desde 1:5 (5 l/kg) hasta 1:10 (10 l/kg) dependiendo de las características estructurales de las máquinas (diseño de máquina).
4. DOSIFICACIÓN DEL COLORANTE
Los colorantes deben ser siempre dosificados; excepto en el laboratorio donde se inicia un baño estático y con poca cantidad de material. La dosificación de los colorantes es de suma importancia, puesto que la introducción de éste en las máquinas de tintura se da por un solo punto, es decir, hay un punto principal de contacto entre el colorante en solución y el material textil y esto se da en la tobera (parte superior de la máquina cercana a cada torre).
La dosificación permite que el colorante se distribuya de manera uniforme en toda la extensión del material (una cuerda de tela puede ir desde los 60 m hasta los 1200 m, dependiendo de la capacidad de la máquina, las características de la tela y la cantidad de rollos armados en una cuerda. La dosificación de los colorantes reactivos se realiza, por lo general a baja temperatura: 40°C – 60°C, excepto los colorantes de muy baja sustantividad, que se realizan a temperaturas superiores (70°C – 80°C).
Esta dosificación a baja temperatura, permite que la energía suministrada sea lo estrictamente necesaria para la difusión molecular, logrando una difusión lenta y homogénea en todo el sustrato.
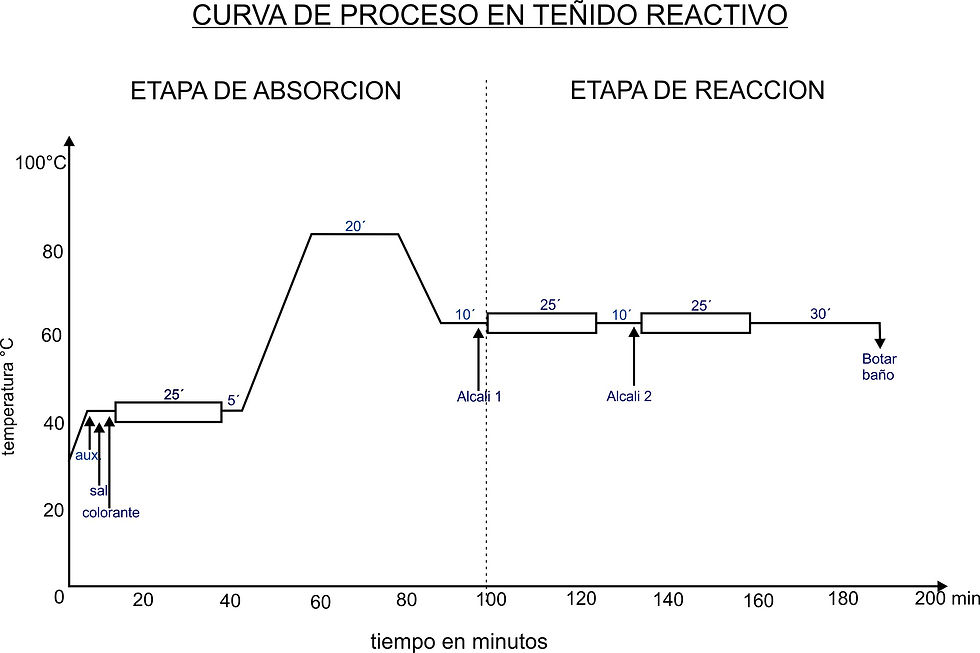
5. ADICIÓN DEL ELECTROLITO (SAL)
Como electrolito se puede utilizar el cloruro de sodio (NaCl) o el sulfato de sodio (Na2SO4); la función principal que cumple el catión sodio (Na+) es neutralizar la carga de la celulosa que en medio acuoso es negativa, por la presencia de radicales (OH-) presentes en su estructura química. Una vez neutralizada la carga del material, la difusión del colorante en el baño hacia el interior de la fibra será garantizada.
En colores claros, la poca cantidad de colorantes presentes en el baño se difunde de manera fácil y rápida hacia la superficie del sustrato textil, motivo por el cual se corre el riesgo de una adsorción irregular en toda la extensión del material textil; por ello volvemos a recalcar el cuidado que se debe tener en la dosificación del colorante.
Para asegurar una homogénea adsorción del colorante sobre el sustrato, en este caso en particular, se debe adicionar el electrolitro una vez culminado la dosificación del colorante, esto garantizará que el colorante distribuido de manera uniforme sobre la superficie textil sean también absorbidas de manera uniforme desde la superficie hacia la parte interna de la fibra.
En colores medios u oscuros la adición del electrolito se realiza antes de la dosificación del colorante o conjuntamente con ello; esto debido a que la alta concentración de colorante permite una absorción uniforme.
Nótese que el electrolito no requiere ser dosificado, debido a su alta solubilidad y difusión en el baño, por lo general se realiza extrayendo el baño de la máquina (baño recirculado con colorantes y auxiliares) sobre éste se disuelve la cantidad de electrolito requerido y se introduce al sistema, esto se realiza con la finalidad de no incrementar la relación de baño (R:B). Sólo en algunos casos como en la tintura con colorantes turqueza o azul royal (R especial) se recomienda adicionar el electrolito con agua fresca; esto con la finalidad de prevenir precipitados (generación de manchas sobre el material).
La cantidad de electrolito a utilizarse van desde 20 g/l (colores claros) hasta 100 g/l en colores con alta concentración de colorantes (colores oscuros), esto claro está con el uso de cloruro de sodio (NaCl); con el sulfato de sodio (Na2SO4) la cantidad a usar es menor dado que una mol de sulfato de sodio contiene el doble de iones de sodio (Na+) respecto al cloruro de sodio, es decir para el mismo peso de sal el sulfato tiene el doble de actividad ionica.
6. MODULACIÓN DE LA TEMPERATURA
La acción de la temperatura sobre los colorantes durante la tintura permite entre otras cosas la mejor difusión de los colorantes del baño de tintura hacia el material textil, mejora el rendimiento tintóreo y actúa como agente de migración.
Se debe iniciar la tintura, en forma general, a baja temperatura 40°C – 60°C salvo algunas excepciones (colorantes de baja sustantividad inician el teñido a temperaturas mayores 70°C – 80°C). Luego de la dosificación del colorante y la adición del electrolito se da un tiempo de igualación no menor a 20 minutos, antes de la dosificación del álcali. En algunos colores denominados críticos, donde la compatibilidad no está garantizada (beige, grises, brown, verde olivo, etc.) se diseñan curvas de tintura denominadas migratorias; es decir se eleva una temperatura prudente (80°C por ejemplo) y se mantiene durante 15 a 20 minutos, luego se enfría a 60°C para su fijación con álcali. Esto permite homogenizar de mejor manera los colorantes sobre la fibra antes de su fijación o reacción química.
En la etapa de fijación (etapa de reacción química) la dosificación del álcali se debe realizar a baja temperatura 60°C, esto para prevenir una fijación súbita con consecuencia de mala igualación; hay excepciones cuando se trabajan con colorantes de baja reactividad en el cual se realiza la fijación a temperaturas mayores 80°C por ejemplo.
Les sugiero que profundicen en el análisis de los tipos de colorantes existentes, hoy en día la clasificación de los colorantes reactivos está dada por:
Grupo vinil sulfon (colorantes que trabajan en frío) ejemplo 60°C con isoterma.
Grupo monoclorotriazina (colorantes que trabajan en caliente) ejemplo 80°C con isoterma. De poco uso en la actualidad.
Grupo bifuncionales, los más utilizados en la actualidad, operan en un rango variable de temperatura, desde 40°C a 80°C.
Dentro de estos grupos van a encontrar diversos colorantes y tienen características diferenciadas de sustantividad y reactividad. El análisis detallado permite diseñar curvas de tintura confiables, reproducibles y mejoran la compatibilidad, considerando que en la mayoría de los casos una tintura lleva 3 colorantes (amarillo, rojo y azul) y éstos deben ser compatibles.
De no encontrar información, de acuerdo a sus comentarios, profundizaremos en otro artículo sobre este tema de clasificación de colorantes reactivos.
7. DOSIFICACION DEL ALCALI
El álcali juega un rol muy importante en el teñido con colorantes reactivos, esta sustancia permite formar una reacción química entre la celulosa y la parte reactiva del colorante a través de un enlace covalente (que es una unión fuerte a nivel molecular). Se utiliza el carbonato de sodio (Na2CO3) o también denominado soda ash, es un álcali débil que permite variar el pH del medio tintóreo de 7 hasta 10.5, en este pH se produce la reacción química entre el colorante y la celulosa. Lo más importante en esta etapa es que la introducción del álcali sea dosificada, en un tiempo prudente que por lo general es 25 min; si el tiempo de rotación de cuerda es menor a 2 min podría considerarse una dosificación entre 15 a 20 min y si el tiempo de rotación es mayor a 2 minu, entonces debemos pensar en dosificar el álcali de manera más extendida. Se estila realizar en 2 dosificaciones de 25 min cada una, interrumpidas por un tiempo de igualación de 10 min, esto permite una óptima igualación de la tintura, por ello es necesario que la elevación del pH en el baño sea gradual.
En los colores oscuros o formulaciones con colorantes del grupo vinilsulfon se requiere elevar el pH a 11.0 u 11.5; esto solo con la adición de carbonato de sodio no es posible, para ello se le acompaña de soda caustica (NaOH) o potasa caustica (KOH) que son álcalis fuertes. Una receta sugerida puede ser: 5 g/l de Na2CO3 (Carbonato de sodio) + 2 g/l de NaOH (soda caústica).
Hago la salvedad que en algunos países donde el carbonato de sodio es una sustancia restringida se utiliza con mucha frecuencia el alcalígeno, que es potasa caustica en disolución, en este caso en particular se debe controlar las dosificaciones y la cantidad de gramos litros (g/l) a utilizar, debido a que esta sustancia no deja de ser un álcali fuerte cuya reactividad es muy alta.
8. TIEMPO DE AGOTAMIENTO

Se conoce como agotamiento la parte final de la tintura comprendida dentro de la etapa de reacción; una vez dosificado el álcali es prudente darle un tiempo adicional de igualación y reacción, y esto depende de la cantidad de colorante adicionado a la tintura (intensidad del color). Antes de botar el baño, en un color claro puede extenderse 20 min de agotamiento; en un color medio 30 min y en un color oscuro un máximo de 60 min; esto permite el mayor aprovechamiento del colorante mediante la maximización de la reacción entre el colorante y la celulosa.
Cabe mencionar que en colores medios y oscuros en usual encontrar coloración en el baño residual de tintura, pese a los tiempos antes señalados, esto debido a que no todo el colorante adicionado a la tintura reacciona con la fibra celulósica, los colorantes tienen un máximo rendimiento que en la mayoría de los casos, van del 65% - 80%; por lo tanto lo que se observa en el baño son colorantes hidrolizados, que ya no son posibles de reaccionar y que deberán ser eliminados.
9. CONTROLES ANTES DEL ENJABONADO
Una vez culminada la etapa de tintura se bota el baño, seguido de enjuagues a baja temperatura (la temperatura de los baños de enjuague y neutralizado nunca deberán ser superior a la temperatura de teñido). Luego se neutraliza con un ácido orgánico que generalmente es el ácido acético (CH3COOH), esto para bajar el pH hasta 6.5 – 7.0, que son condiciones esenciales antes de realizar el enjabonado. Asimismo es importante bajar la concentración del electrolitro a rangos menores a 1 g/l ya que en concentraciones mayores la carga ionica presente por efecto del Na+ hace que los colorantes hidrolizados permanezcan atraídos por la fibra y sea difícil su eliminación; en consecuencia el material textil teñido tendrá una baja solidez al lavado (esto se presenta en colores oscuros).
Se exige que el pH sea neutro (pH = 7) o ligeramente acido (pH = 6.5) debido a que en rangos ácidos o alcalinos determinados colorantes son sensibles a la hidrólisis ácida o hidrólisis alcalina; por tanto en el enjabonado que se realiza a temperaturas de hervor se destruyen parcialmente los cromóforos, con la consecuencia de un cambio de tonalidad; por ello es importante controlar los dos parámetros arriba mencionados.
10. ENJABONADO O ELIMINACION DEL HIDROLIZADO
Esta es la última etapa del teñido con colorantes reactivos, la finalidad del enjabonado es eliminar los colorantes remanentes que no pudieron reaccionar o fijarse con la celulosa, debido a que en el proceso sufrieron rupturas internas producto de la hidrólisis (hidrólisis= fraccionamiento de una molécula por la acción del agua).
Para eliminar estos colorantes no deseados que en muchos casos llegan a estar presentes hasta en un 35% de la cantidad inicial de colorantes (colores oscuros), se requiere llevar a temperatura de ebullición (esta temperatura depende de la altitud a la cual se encuentre la localidad, ejemplo en Lima el agua hierve a 98°C, en la Paz = 85°C, Guatemala = 90°C). Es la temperatura óptima para eliminar los hidrolizados, si se trata de un color claro en el cual se ha adicionado poca cantidad de colorante, basta realizar el enjabonado con sólo agua y el material se verá fácilmente liberado, del mismo modo se puede realizar el enjabonado a baja temperatura, por ejemplo a 80°C por un periodo de 10 a 15 min.
En los colores oscuros se hace imprescindible realizar el enjabonado a temperatura de ebullicion, manteniéndolo por un período de 10 min y se acompaña con un agente jabonador, que puede ser un secuestrante o un auxiliar químico a base de poliacrilatos, que permiten la fácil remoción del colorante hidrolizado contenido en las fibras. Por otro lado habrán colores con alto contenido de hidrolizados que ameriten hacer un doble jabonado (repetir la fórmula y la curva), siempre es recomendable hacer un enjuague adicional en frío después del enjabonado, esto para eliminar rastros de espumas u otros residuos que podrían perjudicar la calidad de nuestro teñido.
Para mejor control de la solidez se realiza en el Laboratorio una simulación de lavado doméstico, siguiendo la descripción de la norma AATCC 61.
__________________
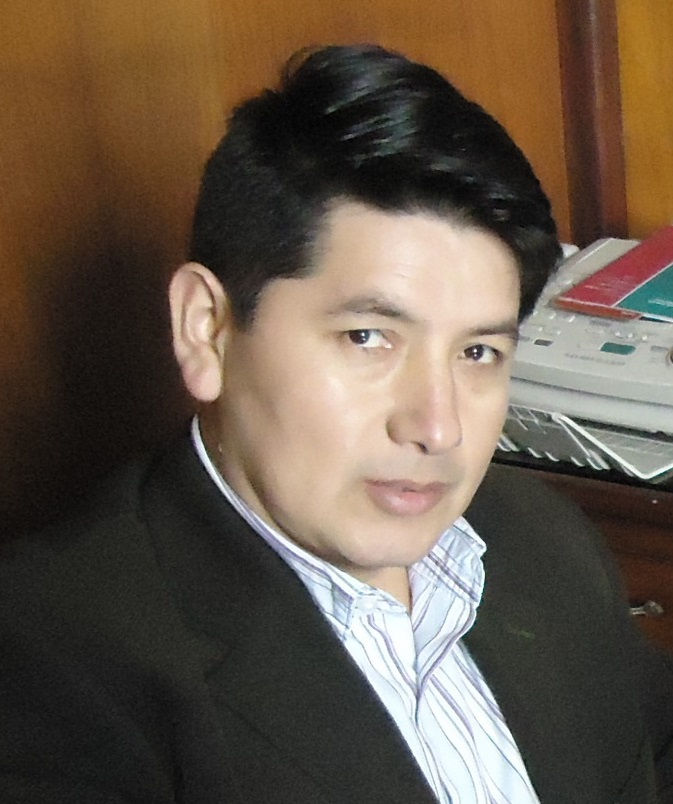
Autor del artículo: Ing. Arnaldo Peña Cabello.
Ingeniero Químico especializado en Gestión de Procesos Químicos Textiles.
Director del Instituto Privado de Tecnología Textil.
E-mail: capacitaciones@ipttperu.com
Web: https://www.ipttperu.com/expositoresiptt
Comentarios